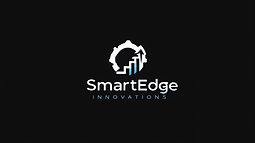
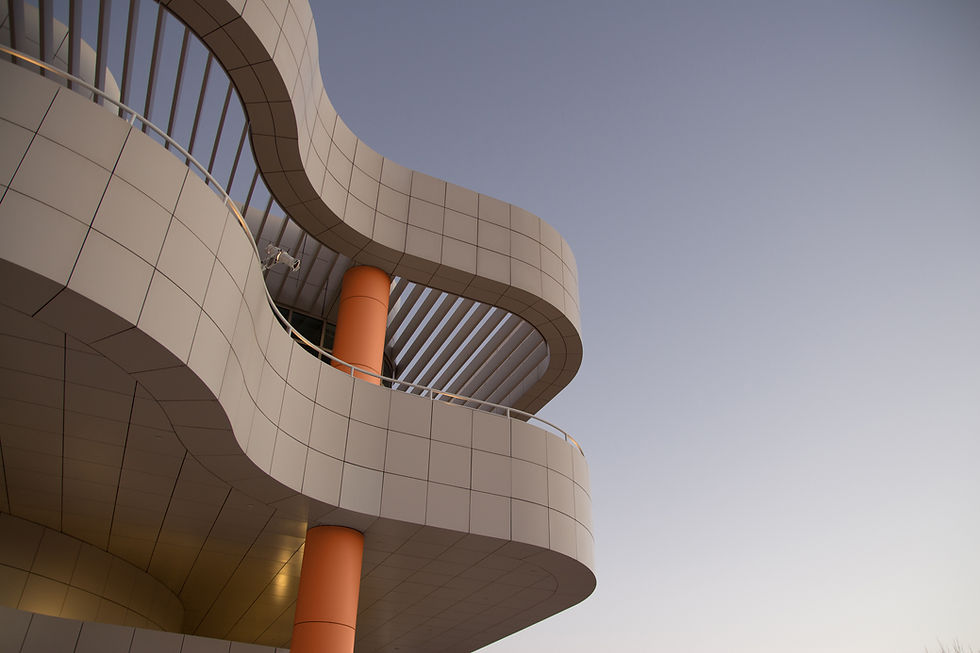
The Real Cost of Inefficiency in Small-to-Mid-Sized Warehouses
2
8
0
By Colleen Stewart | Supply Chain Consultant | April 2025

In the world of logistics, efficiency isn't a luxury—it’s survival. For small to mid-sized warehouses, every misplaced item, every delayed order, and every inefficient process comes at a price. But how much is inefficiency really costing your business?
The answer: more than you think.
🔍 Hidden Costs Are Everywhere
Most warehouse leaders focus on obvious expenses: labor, space, and equipment. But inefficiency hides in the gaps between systems and people:
Idle Labor Time – If your team spends 15 minutes per hour waiting for instructions, system updates, or inventory to arrive, that’s over 12.5% of wages paid for zero output.
Inaccurate Inventory – Misplaced SKUs lead to backorders, customer complaints, and lost sales.
Space Waste – Poor layout or slotting often results in wasted square meters and higher rent costs.
Order Delays & Errors – Rework, customer churn, and reputation damage aren’t always tracked—but they hurt your bottom line.
💡 Case Study
One client—a mid-sized FMCG warehouse—believed their operation was “doing fine.” But after a one-day walkthrough, we identified:
18% of picking time lost due to poor slotting.
Inbound shipments delayed an average of 42 minutes/day due to unclear staging zones.
12% of inventory overstocked due to lack of visibility.
After applying low-cost, high-impact improvements? They saved over €74,000 annually.
🚨 The Myth: “We’re Too Small for Optimization”
Many small businesses assume that efficiency improvements are reserved for large, automated operations. That’s simply not true.
With simple tools like:
Visual SOPs
Slotting maps
Labor tracking via whiteboards or tablets—you can unlock 15–30% more productivity with minimal cost.
✅ Quick Self-Check: Are You Losing Money Here?
Ask yourself:
Do we know our average pick time per order?
Are replenishments interrupting active picks?
Is our receiving area slowing down throughput?
Do our employees rely on “tribal knowledge” to get things done?
If you answered “I’m not sure” to any of those… you likely have hidden inefficiencies bleeding profit.
📥 Bonus: Download the Free Efficiency Checklist
I’ve created a free 1-page Warehouse Efficiency Checklist you can use to audit your own operations.
👋 Ready for a Second Pair of Eyes?
Sometimes all it takes is a short walkthrough with an expert to uncover what’s holding your warehouse back.
Let’s connect—book a free 20-minute strategy call and I’ll show you where you could save time, money, and stress.